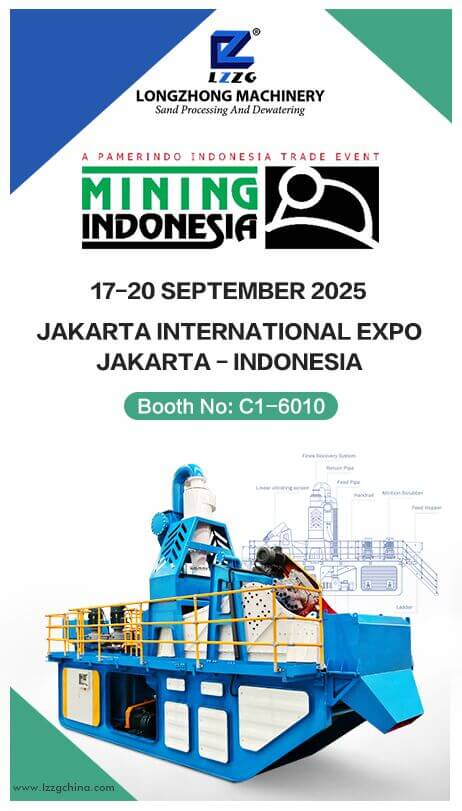
Mining Indonesia 2025
Exhibition Name: The 23rd International Mining & Mineral Rec…
Tel: 86-18736301510
Fax: 86-379-65160018
Email: export@lylzzg.com
2022-05-23
During the working process, there are many fatigue cracks in the linear vibrating screen, mainly on the side plate, bottom beam, girder, and other components. Through the analysis of the reasons of each part, the corresponding reinforcement and anti-cracking measures are proposed for each part, and the implementation effect has been very good in practice.
The vibrating screen mainly causes the movement of objects on the screen through the vibration of its screen, so as to screen the materials smaller than the screen holes to the bottom of the screen to achieve the purpose of separating objects of different sizes. The vibrating screen has the advantages of simple structure, convenient maintenance and high efficiency, and is widely used in mining, coal, chemical, and other industries for its excellent ore screening.
1. Cracked side panel
The main positions of the side plate cracking can be roughly divided into along the vibration direction and perpendicular to the vibration direction. When the crack of the side plate is the former, it is reinforced by adding a square sub-plate within 200mm around the crack. When the cracking is the latter, it is necessary to reinforce the side plate as a whole, and deal with the overall riveted sub-plate, because if it is not handled in time, the overall side plate will break.
2. Cracks occur in the middle of the bottom beam
Because the bottom beam is subjected to the collision and vibration of the raw coal for a long time, the middle part of the bottom beam is more prone to cracks. At this time, it is necessary to make grooves on the cracks, and at the same time weld the grooves flat, and plug welding and Intermittent welding welds the auxiliary plate to the bottom beam to increase the strength of the bottom beam and prolong its service life.
3. Cracks in the beam of the exciter
The exciter is the main device of the whole vibrating screen, and its girder plays a particularly critical role. Although it will be specially strengthened in the design, cracks will also occur after long-term use. thickness of the groove, and weld the groove flat. During welding, the welding workers are required to accurately control the welding rod, welding temperature and welding time. After the welding is completed, the auxiliary plate is welded at the crack, and if necessary, the reinforcement ribs are welded on the auxiliary plate to maximize the strength of the exciter beam. Fatigue resistance and prolong its service life.
4. Cracks occur in the baffle plate of the feeding port
The main reason for the crack of the inlet baffle is that the material cannot be accurately dropped on the blind plate. By adjusting the angle and height of the material inlet, the material can be accurately dropped to the blind plate. When cracks occur, they can be strengthened with channel steel, square pipes, etc.
5. Cracks occur in the baffle plate of the discharge port
The main reason for the cracks in the baffle of the discharge port is that the material moves for a long time, so that the baffle of the discharge port is worn and thinned. The baffle assembly of the discharge port can be surfacing to the original thickness, and then the welding part can be ground flat. If necessary, the discharge port can be heat treated to enhance the wear resistance of the discharge port.